
FAQ
- Is it possible for you to accept our order of making mold die(s) only, not the whole process from making mold dies to mass production of molded items?
- Sure. No problem even if your order is only for making mold dies. We're able to make any types of mold dies for you to use for domestic production or for overseas production.
- How long do we have to wait for getting price estimation from you?
- Usually one(1) or two(2) days from the date of your inquiry.
- What is your usual lead-time until your delivery of our order for mold dies?
- Usually two(2) or three(3) weeks for trial mold dies. About one (1) month for mass-production mold dies.
If you need them much earlier, please inform us in advance. We'll try our best to meet your needs as much as we can in this case.
- Is it possible for you to accept our order of trial molding only?
- Sure. No problem. We also accept your trial molding with mold dies provided by your side.
- Is it possible for you to accept our request for repairing mold dies supplied by other makers?
- Sure. No problem. After our repairing, we make trial molding using the repaired mold dies.
So, Please rest assured about such repairing.
- Are you able to machine or process any types of materials?
- Yes. We're able to machine or process a wide variety of materials like iron, aluminum, stainless steel, copper alloy, carbide metals, ceramic materials and many others.
- Are you able to accept our order for surface-plating?
- Yes. No problem. We are able to do surface-plating for you. Call us when you need it.
- Do you sell your Compact Molding Machines?
- Yes. We sell them. Before you purchase it, we need to discuss with you for detailed specifications.
- We would like to request you to mass-produce our plastic items. Is this possible for you?
- Sure. We're happy to mass produce them. First, please contact us for details. We are ready to give you price estimation for the mass production.
- Is it possible for you to accept our order for machining our parts?
- We are ready to machine your parts for you. Our factories are well-equipped with gun drills and other devices for machining.
- What kind of resins are you able to mold?
- Many kinds. For example, Ultra-Low Viscosity Liquid Silicone Rubber (PDMS), Fluororesin, Polylactic Acid, and more kinds. We have ever proudly made mold dies for these specific resins and done molding for our customers.
Glossary
Terms related to Mold Die
- Cartridge Heater
- "Cartridge Heater" is a heating element made of metal tube designed for heating a mold die.
- Cavity
- "Cavity" is a hollow area within an injection mold die in which a product is molded. Sometimes, cavity refers to a female mold die, named "Cavity Plate", which forms such hollow area.
- Core
- "Core" is a projection (male mold die) designed for creating the inside of an molded item.
- Ejector Pin
- "Ejector Pin" is a pin inside the mold die to push an molded item out from the mold die.
- Electric Discharge Machining
- "Electric Discharge Machining" is one of the machining methods: This method is to use arc discharge, which is repeated in a short frequency between an electrode and the subject, for removing partially the surface of the subject.
- Gate
- "Gate" is an inlet through which melted molding materials run into the cavity.
- Grinding Machine
- "Grinding Machine" is a machine that does the grinding by use of a grinding wheel instead of single-point-tool, milling cutter and/or any other cutting tools.
- Hardening
- "Hardening" is one of the heat treatments used for heating iron steel at a very high temperature and then quickly cooling it, which is designed for effectively enhancing its hardness. This heat treatment is applied for any parts which need to be hard enough and wear-resistant enough.
- Hot Runner
- "Hot Runner" is a technology with which we take out molded items only from the mold dies at the time of injection molding. We do this by heating the runner.
- Injection Mold Die
- "Injection Mode Die" is a mold die used for injection molding by Injection Molding Machine. In a normal molding by the machine; First, melted molding materials are poured, through sprue, runner and gate into the cavity of a mold die set in the machine. Second, the materials become cooled and solidificated. Third, the mold die opens automatically after that. Then, the molded die is ejected out from the machine.
- Lathe
- "Lathe" is a machine which turns a subject and grinds it with single-point tool fixed on the machine.
With a lathe, you can do the machining of straight turning, facing, taper turning, inners-boring, hole-boring, parting, tapping and many others.
- Machining Center
- "Machining Center" is a computer numerical control machining apparatus. Machining Center is equipped with different tools and functions, which are automatically changed for different machining purposes. So, one unit of Machining Center is able to do milling-cutting, boring, tapping and other different machining work. Various cutting/milling tools are stored in its tool magazine. Machining Center does machining automatically by receiving an order from its computer numerical control.
- Mirror Finish
- "Mirror Finish" is one of the finish methods:Buffing, lapping, honing, polishing, ultra-finishing and doing other processing on the surface of mold dies, plastic and other items so that such surface becomes really flat and shiny just like mirror.
- Nitridization
- "Nitridization" is one of the surface-hardening methods designed for making an iron steel excellently wear-resistant and better in some properties. For this purpose, nitride gets penetrated and scattered on the surface of an iron steel for making its surface only hard.
- Parting Line
- "Parting Line" is a section which divides the female and male parts of a mold die or divides the mother part and the side core of a mold die. Parting Line is often called "PL" for short.
- Runner
- "Runner" is a part of the route from the sprue to the gate in molding die, along which melted materials are put into the cavity.
- Sprue
- "Sprue" is a runway for resin to go into an injection mold die. Its cross-section is round-shaped.
- Thermocouple
- "Thermocouple" is a temperature sensor designed to measure the temperature gap to control the temperature in mold die.
- Three-Plate Mold Die
- "Three-Plate Mold Die" is a mold die with three separate sections: fixed side, movable side and "Stripper Plate" in the middle section. When a mold die opens or closes, the die is separated into three sections.
- Two-Plate Mold Die
- "Two-Plate Mold Die" is a mold die with two separate sections: "the side by the injection molding machine"
and "the side that moves when a mold die is opened and closed."
- Undercut
- "Undercut" means the concave and convex part of a molded item, which makes it a little difficult to be taken out from its mold die.
- Wire-Cut Electric Discharging Machining
- "Wire-Cut Electric Discharging Machining" is one of the electric discharging machining methods.
This method is designed for making a 2-dimensional outline. In this method, a wire of 0.03mm~0.3mm diameter is used an electrode. This method is usually used for machining an insert to be used in an injection mold die.
Terms related to Molding & Molding Machines
- Backflow Prevention System
- "Backflow Prevention System" is a system to prevent resin from going back into a plasticizing unit at the time of injection. Different molding machines have different Backflow Prevention Systems. MEIHO's Molding Machines are featured with air-cylinder-driven Shut-off Valve.
- Burning
- "Burning" is a phenomenon that resin is burned by the high heat inside a mold die when the melted resin is injected into the mold die's cavity. At the time of injection, the air inside the mold die becomes compressed and its temperature becomes very high, causing this burning phenomenon.
- Cold Slug
- "Cold Slug" is too sticky resin or hardened resin at the tip-end of the nozzle as the result of mold die contacting the nozzle. To prevent or solve Cold Slug problems, any proper measures such as Cold Slug Well are usually taken. This is because the sticky or hardened resin often chokes the gate at the time of performing a next shot.
- Cooling Time
- "Cooling Time" is the time until the cooling seems to have finished. The melted resin injected into the cavity of a mold die comes to be cooled by conducting its heat to the mold die. The cooling is judged to be over, usually when the temperature of the central area (the thickest area) on both surfaces of the mold die goes under the thermal deformation temperature of the materials injected.
- Cushion Amount
- "Cushion Amount" is the amount of melted plastic remaining in the plunger after the screw moves forwardmost into the front end of injection cylinder. Pressure Retaining Function does not work properly in case of small amount of cushion.
- Dent
- "Dent" is a concave phenomenon which happens on the surface of a molded item.
- Ejector
- "Ejector" is a device which takes a molded item, sprue and runner from a mold die and brings them outside of a molding machine.
- Filling Pressure
- "Filling Pressure" is the pressure at which resin is filled into the inside of a mold die in the injection molding. This pressure is also called Primary Pressure and expressed by kgf/c㎡ or MPa.
- Gate-Cut
- "Gate-Cut" means the cutting of a molded item from the runner. Several ways of cutting are available. For example, cutting by automated machine or manually. In other cases, Gate-Cut is performed within a mold die for the purpose of making the whole molding process short.
- Hopper
- "Hopper" is a container attached to a molding machine. This is for supplying molding materials to a molding machine.
- Injection
- "Injection" means pushing out melted resin by plunger.
- Injection Compression Molding
- "Injection Compression Molding" is a method of molding as follows:When resin is being filled, the cavity is a little bit expanded. After the completion of the filling, a molded item is pressured for molding by use of Mold Die Clamping System and Hydraulic Cylinder inside a mold die. In this method, molecules orientation hardly occurs, the remaining pressure decreases and deformed items less often happen.
- Injection Molding
- "Injection Molding" is a molding method as follows: First, heat plastic materials into liquid. Second, pour the liquid plastic materials into a mold die by use of injection pressure and fill the materials into the mold for molding.
- Injection Pressure
- "Injection Pressure" is the pressure at which resin is injected.
This pressure is expressed by kgf/c㎡ or MPa.
- Injection Rate
- "Injection Rate" is a theoretical injection volume per unit time. This rate shall be calculated by multiplication of the cross-section area of the screw or the plunger and the strokes.
- Injection Speed
- "Injection Speed" is a stroke per plunger's unit time when an injection molding machine fills melted plastic materials into a mold die. This Injection Speed is expressed by mm/sec.
- Injection Volume
- "Injection Volume" is the volume or the weight of molding materials which can be injected one time by an injection molding machine in its injection process.
- Inner Pressure in Cavity
- "Inner Pressure in Cavity" is a pressure that is applied onto the cavity at the time of injection molding.
- Liquid Silicone Rubber
- "Liquid Silicone Rubber" is siloxane bond (Si-O-Si), in which its major skeleton is bonded with silicone and oxygen one after another, with organic base also attached. Liquid Silicone Rubber has excellent unique properties; strong against high / low temperature, difficult to be aged under UVR, water-resistance, etc. This Liquid Silicone Rubber can be changed into various forms: oil, resin, liquid rubber, rubber and others, so this has been used in a wide variety of fields including transportation machines, chemicals, textiles, food, cosmetics, construction and many others.
- Mold Die Clamping Force
- "Mold Die Clamping Force" is the pressure, which is applied to a mold die, designed for keeping the mold die closed. This pressure is against the one from filled melted pressure.
- Mold Die Clamping Method
- "Mold Die Clamping Method" is a method of closing a mold die in an injection molding machine.
There are two methods available: Toggle Type and Direct-Pressure Type.
- Mold Die Closing Time
- "Mold Die Closing Time" is the period of time from when a mold die starts to close and to when the mold die completely closed.
- Mold Die Opening Time
- "Mold Die Opening Time" is the period of time from when a mold die starts to open and to when the mold die completely opened.
- Mold Die Temperature
- "Mold Die Temperature" is the set temperature or actually measured temperature in a mold die.
"Mold Die Temperature" greatly influences melting, filling and hardening of molding materials. The temperature also influences the quality of a molded item and molding cycle time. So this temperature is a very important factor for molding.
- Mold Die Thickness
- "Mold Die Thickness" is the thickness of a mold die which can be attached to a molding machine.
- Molding Cycle
- "Molding Cycle" is defined as "Unit Time" from when one time of injection molding process starts and to when it is completed.
- Nozzle
- "Nozzle" is a parts through which resin is injected from a molding machine. It gets in contact with the sprue push of a mold die.
- Nozzle Touch Force
- "Nozzle Touch Force" is the force by which the sprue push of a mold die and the nozzle get in contact with each other.
- PDMS
- "PDMS" is a type of liquid silicone (about 5Pa・s) of low viscosity and high purity. "PDMS" is excellent in solvent-resistance, old-resistance, chemical-resistance and heat-resistance. Since it has no self-luminescence, it is expected to be used as a good substitute for glass used in micro-chemical chips. A lot of attention has been directed to "PDMS" for its excellent property.
- Plasticization
- "Plasticization" is to melt plastic materials by applying heat and pressure on them and get them liquefied.
- Platen
- "Platen" means the movable plate and the fixed plate used in a molding machine.
- Plunger
- "Plunger" is a tubular item which reciprocates inside the cylinder in the injection unit and pushes out the melted resin.
- Purge
- "Purge" is a function to remove, by activating the screw and the plunger, all the materials from the heating cylinder of a molding machine. At the time of replacing molding materials with new ones for next molding work, you have to remove all the remaining and previous materials from the inside of the molding machine and clean completely the inside of the molding machine for setting molding materials.
- Retention Pressure
- "Retention Pressure" means the pressure to be applied until the gate becomes solid enough after melted resin is filled into a mold die in injection molding process. This pressure retained for the gate solidification is different from injection pressure and is adjustable. This Retention Pressure prevents molding materials in the cavity from backflow and also prevents the filling pressure from reducing. This Retention Pressure also helps the molding materials to be cooled and contracted smoothly. Thus, Retention Pressure helps the adjustment of molded item's shape and its dimensions.
- Runny-Nose Leakage
- "Runny-Nose Leakage" is a phenomenon that resin leaks from the inside of the cylinder and runs out from the nozzle just like runny nose. To prevent this leakage, Suck-Back must be taken as a preventive measures.
- Screw Replasticizing Type Injection Molding Machine
- "Screw Replasticizing Type Injection Molding Machine" is a molding machine of the following system:
First, get molding materials plasticized in a special plasticizing screw. Second, forward the materials to the front part of the plunger. Then, move the plunger forward for injection purpose.
- Screw-In-Line Type Injection Molding Machine
- "Screw-In-Line Type Injection Molding Machine" is a molding machine, the screw of which is equipped with both plasticizing function and injection function.
- Short Shot
- "Short Shot" is a phenomenon that a molded item becomes defective; Its parts becomes missing. This is because resin is not fully filled inside a mold die. When the resin is cooled and solidificated, its parts is missing and the molded product becomes defective.
- Silver Streak
- "Silver Streak" is a phenomenon that silver-colored, shiny streaks appear on the surface of a molded item. This phenomenon occurs due to somewhat wet materials, thermal decomposition of materials used for molding.
- Speed Reaching Time
- "Speed Reaching Time" means the time it takes the actual injection speed to reach the set injection time.
- Staying Time
- "Staying Time" is a period of time from when molding materials get into Heating Cylinder to when the materials get out from the cylinder. If Staying Time takes longer than necessary, molding materials especially of poor thermostability become carbonized and so defective-contaminated or poor-molded.
- Suck-Back
- "Suck-Back" is to move the plunger and other units a little backward after the completion of weighing.
Suck-Back is designed for preventing any leakage of resin from the nozzle and lowering the pressure of the nozzle.
- Super Engineering Plastic
- "Super Engineering Plastic" is some specific types among the resins defined as "Engineering Plastic" that have specially excellent properties and can be used for a long period of time. Plus their heat-resistance temperature shall be 150℃ or more.
- Temperature Adjuster
- "Temperature Adjuster" is a device that has a heating system inside it and is able to adjust or keep the temperature of a mold die. This adjuster uses water, oil or any other proper material to heat and circulate inside the mold for the purpose of adjusting or keeping the temperature.
- Tie-Bar
- "Tie-Bar" is a support or frame which supports the template of a molding machine, guiding the opening and closing movement of a molded die and receives the mold die clamping.
- Warp
- "Warp" is a deformation of a molded item due to the contraction and relaxation of internal stress inside the molded item.
- Weighing
- "Weighing" is a process, after Pressure Retaining Process, of weighing the amount of the resin for the next shot. In case of Preplasticization Type Injection Molding, the screw does not move at time of weighing, comparing to In-Line Type. So, if you adopt Preplasticization Type Injection Molding, all the molding materials used are evenly plasticized, enabling stable weighing.
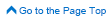